Smart Mittelstand
Warum die Smart Factory nicht nur die großen Player interessieren sollte.
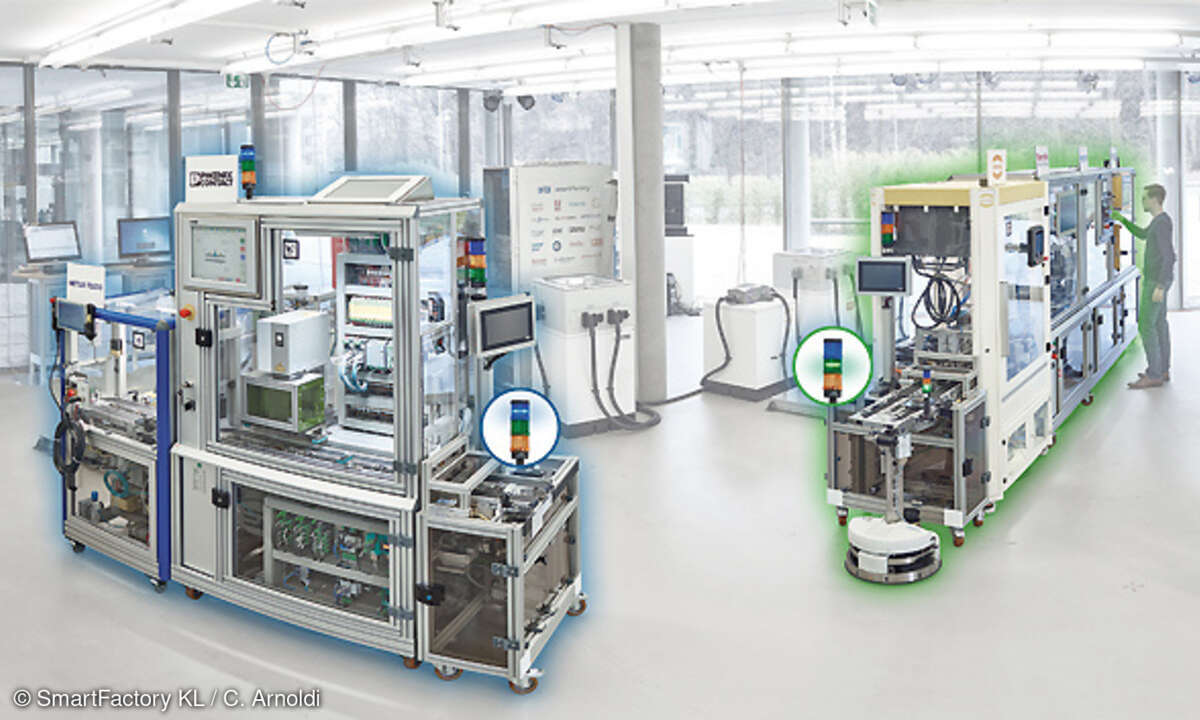
- Smart Mittelstand
- Neue Dynamik durch den Einsatz von KI-Technologien
Die digitale Revolution hat die deutsche Industrieproduktion längst erreicht. Während die großen Unternehmen schon länger auf KI, Robotik und smarte Fabriken setzen, haben Mittelständler oft noch Berührungsängste mit der neuen digitalen Welt – gerade wenn es um die Produktion geht. Worauf kleinere und mittlere Unternehmen(KMU) achten sollten, wenn sie ihre Produktion intelligenter steuern wollen.
Kommt die vierte industrielle Revolution im Mittelstand an?
Der Mittelstand ist der vielbeschworene Motor der deutschen Wirtschaft. Ob einfacher Handwerksbetrieb oder Hidden Champion in der Produktion, der Wirtschaftsstandort Deutschland basierte in der Vergangenheit auf einer ausgeprägten KMU-Landschaft. Laut Bundesministerium für Wirtschaft und Energie wird rund 35 Prozent des gesamten Umsatzes der Unternehmen in Deutschland von KMU erwirtschaftet. Industrie 4.0, also die Digitalisierung der industriellen Produktion, ist in zahlreichen Unternehmen längst Realität. Einer aktuellen Studie des Branchenverbandes Bitkom zufolge nutzen oder planen bereits 71 Prozent der Unternehmen Industrie-4.0-Anwendungen, jedoch werden in der Regel nur einzelne Projekte in Angriff genommen.
Eine Strategie für das Gesamtunternehmen fehlt oftmals. Laut dem „Deutschen Industrie 4.0 Index“ der Beratung Staufen unterhalten nur neun Prozent eine smarte Fabrik, also voll vernetzte und sich selbst steuernde Maschinen. Gerade KMU haben häufig Schwierigkeiten bei der Umsetzung von Robotik und Co – das könnte Auswirkungen auf den gesamten Wirtschaftsstandort haben. Will man auch in Zukunft wettbewerbsfähig bleiben, so ist der Schritt in die Digitalisierung alternativlos.
Daten machen den Unterschied
Sensoren und IP-fähige Geräte werden schon in wenigen Jahren die Fabriken dominieren, Stichwort Industrial Internet of Things (IIoT). Über Datensammlungen werden so schlankere Prozesse geschaffen, Abläufe rationalisiert und die Kosteneffizienz gesteigert. Ein Beispiel hierzu ist die Gerätewartung: Im vernetzten IIoT-Ökosystem können Maschinen untereinander Meldungen kommunizieren, den eigenen Betriebsstatus oder -störungen mitteilen, und so die Produktion untereinander intelligent aufteilen, was einen insgesamt störungsfreien Produktionsprozess gewährleistet.
Dieses einfache Beispiel behandelt nur eine Produktionslinie innerhalb einer einzelnen Fabrik. Das volle Potential lässt sich jedoch erst ausschöpfen, wenn mehrere Standorte über ein Cloud Enterprise Resource Planning (ERP)-System verbunden sind. So digitalisierte Produktionsstätten erreichten in den USA Effizienzsteigerungen von durchschnittlich 82 Prozent. Mit IIoT erhalten Unternehmen Zugriff auf eine wachsende Menge an anlagenbezogenen Daten. Nach den derzeitigen Standards nutzen die Betreiber diese Informationen, um von ihren reaktiven Wartungsaktivitäten zu einer Instandhaltung mittels präziser Vorhersagemodelle überzugehen.
Das Haupthindernis bleibt jedoch weiterhin die Implementierung einer effizienten Wartungspriorisierung über mehrere Standorte hinweg. Dies schafft die Voraussetzungen für den Einsatz von TPM-Aktivitäten (Total Productive Maintenance). Das Ziel dieses in den 50er-Jahren entwickelten Programms ist die Eliminierung von Verlusten und Verschwendung mit dem Ziel von null Defekten, null Ausfällen, null Qualitätsverlusten und null Unfällen in der Produktion. Durch die Kombination von CMMS-Software (Computerized Maintenance Management System) und den über IIoT gesammelten Daten kann das Wartungspersonal Anlagengruppen überwachen, Parameter für die Auslösung von Warnmeldungen festlegen, Maßnahmen automatisieren und Arbeitsaufträge generieren, indem es direkt mit dem Cloud ERP verbunden ist.